Preshipment Inspection: Your Shield In Global Trade
In the intricate dance of global commerce, where goods traverse continents and supply chains stretch across vast oceans, ensuring product quality and compliance is not just a best practice—it's a fundamental necessity. This is precisely where the critical process of preshipment inspection steps in, acting as an indispensable safeguard for businesses and consumers alike. Without robust quality control measures implemented before goods even leave the factory floor, companies risk facing costly returns, damaged reputations, and severe financial repercussions.
Navigating the complexities of international trade demands vigilance and a proactive approach to quality assurance. From raw materials to finished products, every stage of the manufacturing and shipping process carries inherent risks. A comprehensive preshipment inspection program is designed to mitigate these risks, offering peace of mind and fostering trust in a marketplace that thrives on reliability and transparency. It’s about much more than just checking boxes; it’s about building a foundation of confidence in every transaction, ensuring that what was promised is precisely what gets delivered, safeguarding investments and upholding standards in an ever-evolving global economy.
- Unraveling The Mystery What Happened To Dr David Jeremiah
- Aishah Sofey S
- Is Dana Perinos Husband Sick
- Beatrice Mccartney
- Nautica Malone
Table of Contents
- Understanding Preshipment Inspection: A Global Necessity
- Why Preshipment Inspection is Non-Negotiable for Businesses
- The Comprehensive Preshipment Inspection Process
- Key Types of Preshipment Inspections and Their Focus
- Navigating Challenges in Preshipment Inspections
- Choosing the Right Preshipment Inspection Partner
- The Future of Preshipment Inspection: Technology and Trends
- Preshipment Inspection: A Cornerstone of Sustainable Global Trade
Understanding Preshipment Inspection: A Global Necessity
Preshipment inspection (PSI), often referred to as Final Random Inspection (FRI) or Finished Goods Inspection, is a critical step in the supply chain management process. It involves a thorough, systematic examination of goods before they are shipped from the supplier's factory or warehouse to the buyer. The primary goal of a preshipment inspection is to verify that the products meet the buyer's specifications, quality standards, and contractual agreements, as well as relevant international regulations and safety requirements. This meticulous check is typically conducted when at least 80% of the order has been produced and packed, ensuring a representative sample of the entire consignment is available for assessment.
The scope of a preshipment inspection can be broad, encompassing various aspects of the product and its packaging. Inspectors will typically check for:
- **Quantity verification:** Ensuring the correct number of items are ready for shipment.
- **Workmanship and appearance:** Assessing the overall quality, aesthetics, and absence of defects.
- **Functionality and safety:** Testing the product's operational capabilities and adherence to safety standards.
- **Specifications conformity:** Confirming that the product matches the agreed-upon design, dimensions, materials, and other technical specifications.
- **Packaging and labeling:** Verifying that packaging is robust enough for transit, and labels contain correct information (barcodes, country of origin, warnings, etc.).
- **Shipping marks:** Checking that carton markings are accurate and comply with shipping requirements.
- **Documentation review:** Ensuring all necessary shipping and quality control documents are in order.
In a world where international news and global events, like those reported by major news organizations, constantly remind us of the interconnectedness of economies, the importance of a reliable supply chain cannot be overstated. Just as a trusted news source provides timely and accurate information to a global audience, a thorough preshipment inspection provides vital, actionable data to businesses, allowing them to make informed decisions before significant financial commitments are finalized. It’s a proactive measure that prevents potential issues from escalating into costly problems down the line, reflecting a commitment to quality that resonates with consumers and partners worldwide.
Why Preshipment Inspection is Non-Negotiable for Businesses
For any business engaged in international trade, particularly those sourcing products from overseas, a preshipment inspection is not merely an option but a fundamental requirement for success and sustainability. The reasons are multifaceted, touching upon financial stability, brand integrity, and regulatory compliance. In today's competitive landscape, where information travels at the speed of light—much like instant breaking news alerts—any lapse in quality can quickly become public knowledge, severely damaging a company's reputation.
Mitigating Financial Risks
The financial implications of receiving substandard or incorrect goods can be devastating. Imagine ordering a large consignment of electronic components, only to discover upon arrival that a significant percentage are defective, or worse, entirely different from what was ordered. Without a preshipment inspection, businesses face:
- **Costly Rework or Returns:** Shipping defective goods back to the supplier for rework or replacement is expensive, time-consuming, and can incur additional customs duties and freight charges.
- **Production Delays:** Substandard components can halt production lines, leading to missed deadlines, loss of sales, and penalties for late delivery to end-customers.
- **Inventory Write-offs:** If defects are severe and cannot be remedied, businesses may have to write off entire batches of inventory, resulting in significant financial losses.
- **Disputes with Suppliers:** Resolving disputes over quality issues can be a protracted and costly legal battle, consuming valuable resources and straining business relationships.
A preshipment inspection acts as an insurance policy, catching these issues before they become entrenched problems. By identifying defects or non-conformities at the source, businesses can demand corrective action from suppliers before payment is fully released or before goods are shipped, thereby protecting their financial investment.
Upholding Brand Reputation and Customer Trust
In the digital age, a company's reputation is its most valuable asset. Customers today are more informed and vocal than ever before. A single negative experience due to poor product quality can lead to widespread negative reviews, social media backlash, and a significant erosion of trust. This is particularly true for YMYL (Your Money or Your Life) products, where quality directly impacts consumer safety or financial well-being. For example, if a company sells children's toys, faulty products could lead to injuries, legal action, and irreparable damage to the brand. Similarly, for financial products, errors can have severe consequences.
A robust preshipment inspection program demonstrates a company's unwavering commitment to quality. It assures customers that the products they receive meet high standards, fostering loyalty and positive word-of-mouth. When a business consistently delivers quality, it builds a strong, trustworthy brand image, much like a reputable news organization builds trust through consistent, accurate reporting. This trust is hard-earned and easily lost, making preshipment inspection an essential tool in brand management and customer retention.
The Comprehensive Preshipment Inspection Process
The process of conducting a preshipment inspection is systematic and typically involves several key stages, ensuring thoroughness and accuracy. While specific steps may vary slightly depending on the product, industry, and the inspection agency, the core methodology remains consistent:
- **Booking and Scheduling:** The buyer or importer initiates the inspection request, providing details such as product specifications, order quantity, factory location, and desired inspection date. It’s crucial to schedule the inspection when a significant portion (usually 80-100%) of the order is completed and packed.
- **Inspector Assignment:** An independent, qualified inspector is assigned to the task. This inspector must possess the necessary expertise for the specific product category and be familiar with relevant quality standards and testing protocols.
- **On-Site Inspection:** The inspector travels to the factory or supplier's premises. Upon arrival, they verify the production status and ensure that the specified quantity of goods is available for inspection.
- **Sampling:** Using statistically valid sampling methods (e.g., AQL - Acceptable Quality Limit), the inspector selects a random sample of products from the finished lot. This ensures impartiality and a representative assessment of the entire batch.
- **Detailed Examination:** The selected samples undergo a meticulous examination. This includes:
- **Visual Inspection:** Checking for cosmetic defects, incorrect colors, finishes, or assembly issues.
- **Workmanship Assessment:** Evaluating the overall quality of construction and finishing.
- **Functionality Testing:** Performing tests to ensure the product operates as intended (e.g., power on/off, button responsiveness, motor function).
- **Measurement Checks:** Verifying dimensions, weight, and other physical attributes against specifications.
- **Barcode Scans:** Confirming scannability and accuracy of barcodes.
- **Drop Tests/Stress Tests:** Assessing packaging integrity and product durability during transit simulations.
- **Labeling and Marking Verification:** Ensuring all labels, warnings, and shipping marks are correct and compliant.
- **Packaging Integrity Check:** Inspecting inner and outer packaging for protective qualities and compliance with shipping requirements.
- **Defect Classification:** Any identified defects are categorized (e.g., critical, major, minor) based on their severity and impact on product usability, safety, or marketability.
- **Report Generation:** Following the inspection, a comprehensive report is compiled. This report includes detailed findings, photographic evidence of defects, measurements, test results, and a clear pass/fail recommendation based on the agreed-upon AQL standards.
- **Client Review and Decision:** The report is sent to the client (buyer) for review. Based on the findings, the client decides whether to approve the shipment, request rework, or reject the consignment.
This structured approach ensures that the preshipment inspection provides a clear, objective snapshot of product quality, empowering buyers to make informed decisions that protect their interests and uphold their brand's promise.
Key Types of Preshipment Inspections and Their Focus
While "preshipment inspection" often refers to the final check, quality control throughout the production cycle is equally vital. A comprehensive quality assurance strategy often incorporates several types of inspections at different stages, each serving a unique purpose. These sequential inspections provide a holistic view of the manufacturing process, allowing for early detection and correction of issues, thereby minimizing the risk of a failed final preshipment inspection.
Initial Production Check (IPC)
The Initial Production Check, also known as the Pre-Production Inspection, occurs at the very beginning of the manufacturing process, typically after raw materials have been sourced and before mass production begins. Its focus is on verifying the quality of raw materials, components, and the initial production setup. This early intervention is crucial for preventing widespread defects. Inspectors will check:
- Raw material quality and quantity.
- Initial samples or prototypes for conformity to specifications.
- Production machinery setup and calibration.
- Factory's understanding of product specifications and quality requirements.
Catching issues at this stage can save significant time and money, as correcting problems early is far less costly than fixing them later in the production cycle.
During Production Inspection (DUPRO)
A During Production Inspection takes place when a certain percentage of the goods (typically 20-50%) have been manufactured and are in various stages of completion. This inspection allows for continuous monitoring of the production process and early identification of any emerging quality issues. It's a proactive measure to ensure that production is running smoothly and consistently. Key areas of focus include:
- Monitoring the production line for consistency and adherence to quality standards.
- Checking semi-finished and finished products for defects.
- Assessing the factory's quality control procedures during production.
- Identifying and addressing any deviations from specifications or emerging defects.
DUPRO inspections are vital for complex products or large orders, providing an opportunity to implement corrective actions before the entire batch is produced, thus preventing major delays or rejections during the final preshipment inspection.
Final Random Inspection (FRI)
The Final Random Inspection is the most common type of preshipment inspection, conducted when the entire order (or at least 80%) has been completed, packed, and is ready for shipment. This is the comprehensive quality check that verifies the finished product against the buyer's specifications and international quality standards. The detailed examination outlined in the previous section (quantity, workmanship, functionality, packaging, etc.) is performed during the FRI. This inspection is the last chance to identify and rectify any quality issues before the goods leave the factory, making it an indispensable step for risk mitigation in global trade.
Container Loading Supervision (CLS)
While not strictly a product quality inspection, Container Loading Supervision is often considered part of the broader preshipment inspection process. It occurs at the point of loading the goods into shipping containers. The inspector's role here is to ensure that the correct products, in the correct quantities, are loaded safely and securely into the container, minimizing the risk of damage during transit. This includes:
- Verifying carton quantities against packing lists.
- Checking for any damage to cartons before loading.
- Ensuring proper loading techniques to prevent shifting or damage during transit.
- Sealing the container and recording the seal number.
CLS provides an additional layer of security, confirming that the efforts of the earlier quality checks are not undermined by improper handling or loading, thereby completing the quality assurance loop before the goods embark on their journey.
Navigating Challenges in Preshipment Inspections
While the benefits of preshipment inspection are clear, the process is not without its challenges. Overcoming these hurdles requires careful planning, clear communication, and a robust understanding of international trade dynamics. Just as a major news network navigates the complexities of global politics and diverse communities to deliver accurate information, businesses must skillfully manage the intricacies of their supply chains.
- **Communication Barriers:** Language differences and cultural nuances can lead to misunderstandings between buyers, suppliers, and inspectors regarding specifications, quality standards, or corrective actions. Clear, unambiguous communication, often facilitated by a professional inspection agency, is paramount.
- **Supplier Resistance:** Some suppliers may resist inspections, viewing them as a lack of trust or an unnecessary imposition. Building strong, long-term relationships based on mutual respect and clearly outlining inspection requirements in contracts can help overcome this.
- **Time Constraints:** In fast-paced supply chains, scheduling inspections can be challenging, especially when production deadlines are tight. Proper planning and flexibility from both buyer and inspector are essential.
- **Scope Creep:** Without clear guidelines, the scope of an inspection can expand beyond what was agreed upon, leading to increased costs or delays. Detailed checklists and predefined inspection criteria are crucial.
- **Inspector Competency and Independence:** The effectiveness of a preshipment inspection hinges on the competency, experience, and independence of the inspector. Using a reputable third-party inspection company ensures impartiality and expertise.
- **Geographical Distance:** Managing inspections across different time zones and remote locations requires efficient coordination and reliable reporting mechanisms.
- **Fraud and Bribery:** In some regions, there can be risks of inspectors being bribed or colluding with factories to falsify reports. Choosing accredited, ethical inspection bodies with strict anti-corruption policies is vital.
Addressing these challenges proactively ensures that the preshipment inspection process remains effective and delivers the intended value, safeguarding your investment and reputation.
Choosing the Right Preshipment Inspection Partner
The success of your preshipment inspection strategy heavily relies on selecting the right inspection partner. This decision is as critical as choosing a reliable source for your daily news and international updates; you need a partner that is authoritative, trustworthy, and possesses deep expertise. A reputable third-party inspection company brings impartiality, specialized knowledge, and a global network to the table, making them an invaluable asset in managing your supply chain risks. When evaluating potential partners, consider the following:
- **Accreditation and Certifications:** Look for companies accredited by recognized international bodies (e.g., ISO 17020 for inspection bodies). This indicates adherence to rigorous standards of competence and impartiality.
- **Industry Expertise:** Ensure the inspection company has specific experience and expertise in your product category. A company specializing in textiles may not be the best choice for electronics, and vice versa.
- **Global Reach and Local Presence:** If you source from multiple countries, a partner with a strong global network and local inspectors can offer consistent service and faster response times.
- **Reporting Quality and Transparency:** Evaluate their sample reports. Look for detailed, clear, and objective reports with photographic evidence, clear defect classifications, and actionable recommendations. Transparency in their processes is key.
- **Technology and Innovation:** Does the company leverage technology for scheduling, real-time reporting, and data analytics? Modern tools can significantly improve efficiency and visibility.
- **Ethical Standards and Impartiality:** Verify their commitment to ethical practices and independence. Ask about their anti-bribery policies and how they ensure inspector integrity.
- **Communication and Customer Service:** A good partner will offer clear communication channels, responsive customer service, and a willingness to understand your specific needs and adapt their services accordingly.
- **Cost-Effectiveness:** While cost is a factor, it should not be the sole determinant. A slightly higher fee for a highly reliable and effective service can save you significantly more in the long run by preventing costly quality issues.
By carefully vetting potential partners, you can establish a long-term relationship with an inspection company that acts as a true extension of your quality control team, safeguarding your investments and brand integrity through effective preshipment inspection.
The Future of Preshipment Inspection: Technology and Trends
The landscape of preshipment inspection is continually evolving, driven by technological advancements and the increasing demands of global commerce. Just as news delivery has transformed from traditional cable news networks to instant social media updates and curated digital channels, PSI is embracing innovation to become more efficient, transparent, and predictive. The future of preshipment inspection will likely be shaped by several key trends:
- **Digitalization and AI Integration:** The adoption of digital platforms for booking, reporting, and data analysis is becoming standard. Artificial intelligence (AI) and machine learning (ML) are beginning to play a role in automating defect detection through image recognition, predicting potential quality issues based on historical data, and optimizing inspection schedules.
- **Remote Inspections and Virtual Reality (VR)/Augmented Reality (AR):** While on-site inspections remain critical, remote inspection capabilities, often utilizing live video feeds and AR tools, are gaining traction. This allows buyers to virtually "be present" during inspections, offering real-time oversight and reducing travel costs.
- **Blockchain for Supply Chain Transparency:** Blockchain technology holds promise for creating immutable records of inspection results, certifications, and product origins. This enhances transparency, traceability, and trust across the entire supply chain, making it harder for fraudulent activities to occur.
- **Data Analytics and Predictive Quality:** Collecting and analyzing vast amounts of inspection data can reveal patterns, identify high-risk suppliers or product types, and enable predictive quality control. This proactive approach helps businesses address potential issues before they even arise, moving beyond reactive problem-solving.
- **Sustainability and Ethical Sourcing Audits:** Beyond product quality, preshipment inspections are increasingly incorporating elements of social and environmental compliance. Buyers are demanding verification of ethical labor practices, environmental impact, and sustainable sourcing, making PSI a tool for corporate social responsibility.
- **IoT and Smart Sensors:** Integrating Internet of Things (IoT) devices and smart sensors into products or packaging can provide real-time data on conditions like temperature, humidity, and shock during transit, offering insights into potential damage risks even after the preshipment inspection is completed.
These technological shifts are transforming preshipment inspection from a static, point-in-time check into a dynamic, data-driven, and continuously improving process. Embracing these innovations will be crucial for businesses aiming to maintain a competitive edge and ensure robust quality control in the global marketplace.
Preshipment Inspection: A Cornerstone of Sustainable Global Trade
In conclusion, preshipment inspection is far more than a mere formality; it is an indispensable cornerstone of sustainable and reliable global trade. It serves as a vital protective layer, shielding businesses from significant financial losses, safeguarding their hard-earned brand reputation, and ensuring that consumers receive products that meet stringent quality and safety standards. In an era where global supply chains are increasingly complex and interconnected, the proactive assurance provided by a thorough preshipment inspection is invaluable.
By investing in robust preshipment inspection processes, businesses demonstrate a profound commitment to quality, transparency, and ethical practices. This commitment resonates throughout the entire ecosystem, fostering trust not only between buyers and suppliers but also between brands and their end-consumers. Just as a civic center serves as a hub for community events and public good, preshipment inspection contributes to the overall health and integrity of the global trading community, ensuring fair play and reliable outcomes.
We encourage all businesses engaged in international sourcing to prioritize and integrate comprehensive preshipment inspection into their supply chain management strategy. It’s an investment that pays dividends in reduced risks, enhanced customer satisfaction, and long-term business success. Have you implemented a preshipment inspection program in your business? What challenges or successes have you experienced? Share your insights in the comments below, or explore our other articles on supply chain management and quality control to further fortify your global trade operations.
- King Von Autopsy
- Caitlin Clark Shower
- Samuel Joseph Mozes
- Indian Uncut Web Series
- Is Dana Perinos Husband Sick
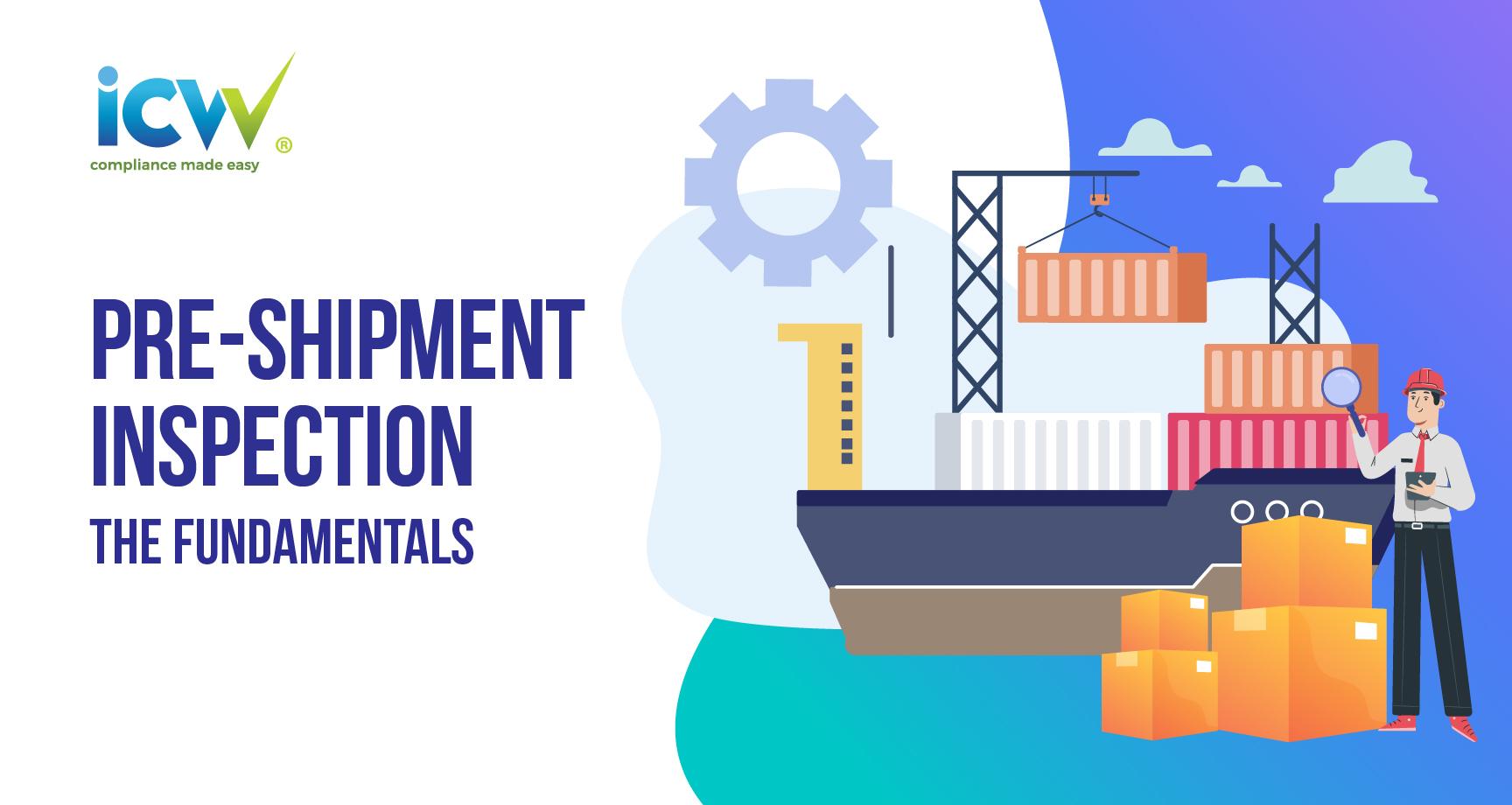
Pre-shipment Inspection | ICW

HardLines Preshipment Inspection - Indo Inspection

HardLines Preshipment Inspection - Indo Inspection